ключевые различия между запорными и шаровыми клапанами
Nov 01, 2024
On this page
Globe valves and ball valves are two commonly used valve types in industrial pipeline systems, each with distinct characteristics in terms of function, structure, and application. The selection between the two valves can significantly impact fluid control, safety, and maintenance costs within the system. Understanding their features and performance benefits helps in choosing the most suitable valve type for specific operating conditions, optimizing efficiency and extending service life.
Globe valves, also known as stop valves, are designed as a type of force-sealing valve. They require external pressure on the disc in the closed position to ensure a tight seal with no leakage. When fluid enters the valve body from below the disc, additional force is needed to overcome the friction between the valve stem and packing, along with the fluid pressure acting on the disc. As a result, the force required to close a globe valve is typically greater than the force needed to open it, necessitating a robust valve stem design to prevent bending or failure.
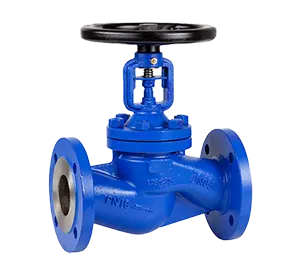
Globe valves utilize a dual-sealing system, combining bellows and packing for enhanced leak prevention. Even if the bellows seal fails, the packing seal continues to effectively prevent external leakage, meeting international sealing standards. This design not only reduces fluid loss and energy consumption but also enhances safety within industrial facilities. The robust bellows seal ensures zero stem leakage, reducing maintenance frequency and operational costs over the valve's lifespan. Additionally, the bellows sealing technology addresses the common issue of aging and leaking with traditional packing, thereby improving reliability and creating a safer, cleaner working environment.
Globe valves are widely used in critical applications that require exceptional sealing performance, particularly in the aerospace sector. In spacecraft, they play a vital role in fluid transport, cutoff, and flow regulation, where reliable sealing is crucial for operational safety and equipment reliability. Studying their sealing characteristics and the influencing factors is important for optimizing valve design and enhancing performance under extreme conditions.
Ball valves control fluid flow by rotating a spherical closure element (the ball). The ball, driven by the valve stem, achieves open or closed states with a simple 90-degree rotation. Known for their ease of operation, low fluid resistance, and excellent sealing properties, ball valves are extensively used in industries such as oil refining, long-distance pipeline transport, chemicals, paper production, pharmaceuticals, water management, power generation, and municipal services.
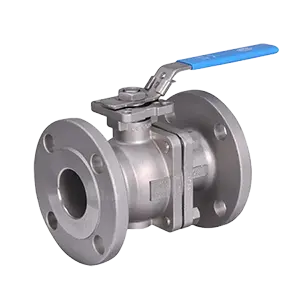
Ball valves are characterized by minimal fluid resistance, with a resistance coefficient comparable to a pipe of the same length. This feature ensures superior fluid dynamics in high-pressure and high-velocity environments. Their simple structure, compact size, and lightweight design make them easy to install and operate. The sealing surfaces, often made of plastic, provide a tight and reliable seal, even in vacuum systems. Ball valves operate quickly and conveniently, with full open or closed states achieved by a 90-degree turn, making them suitable for remote automation. Additionally, the design of the sealing rings allows for easy disassembly and replacement, simplifying maintenance.
Ball valves come in various designs to meet different application requirements. For instance, V-shaped ball valves are ideal for media containing fibers or small solid particles. The strong shearing action between the V-notch ball core and the metal seat ensures smooth fluid flow. Multi-port ball valves, on the other hand, offer flexible media control in pipeline systems, including merging, splitting, and flow direction switching. They can close any port while connecting others, making them suitable for complex scenarios requiring multi-path switching.
When choosing between globe and ball valves, consider the following aspects to make an optimal selection based on operating conditions.
Ball valves offer quick opening and closing with a simple 90-degree rotation and excellent fluid dynamics, making them suitable for high-pressure fluid control with minimal impact on the seat. In contrast, globe valves require a larger rotation angle to adjust flow, making ball valves a better choice for applications demanding precise flow regulation.
Globe valves are generally more durable due to their simple structure but may experience clogging when handling media with solid particles or fibers. Ball valves, with smooth sealing surfaces and minimal impact on the seat, are less likely to get stuck and tend to have a longer service life.
Globe valves require less maintenance due to their straightforward design, making them ideal for low-maintenance applications. While ball valves are robust, their more complex internal structure means that seal replacement and other repairs can be more labor-intensive, requiring more frequent maintenance.
Globe valves are typically less expensive to manufacture, offering a cost-effective option. Although ball valves provide superior performance, their higher cost may not be justifiable in all applications. For budget-sensitive scenarios, globe valves are often the preferred choice.
Globe and ball valves each offer unique advantages and are suited to different applications. Globe valves are valued for their exceptional sealing performance and low maintenance requirements, making them ideal for high-sealing environments such as aerospace and petrochemical industries. Ball valves, with their low fluid resistance, easy operation, and reliable sealing, are widely used in sectors like oil, chemical, and power generation, where quick opening and closing are essential. The choice between these valves should be based on fluid control needs, maintenance capabilities, and budget constraints to ensure system safety, efficiency, and cost-effectiveness.
Cледующий: рекомендации по установке промышленного клапана
Предыдущий: Сбой закрытия электрического шарового клапана: причины и решения
О нас
Продукция
Навигация
Our Contacts
Building 2, NO.59, Songshan Road, SND, Suzhou, China