Обеспечить безопасную и стабильную установку зажимного обратного клапана
Feb 28, 2024
Wafer check valves are essential components in pipeline systems, and their correct installation and regular maintenance are crucial for fluid control and flow protection. Below, we elaborate on the preparatory steps before installation, the installation process, and regular maintenance procedures of the wafer check valve.
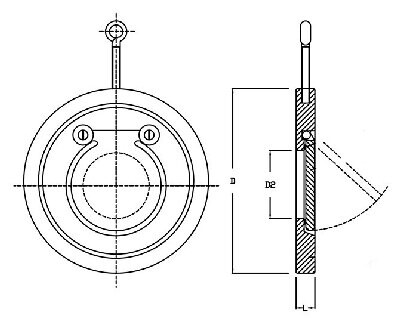
Pre-Installation Preparations
Before proceeding with the installation of wafer check valves, it is essential to undertake thorough pre-installation preparations to ensure a successful and effective installation process. These preparations include:
Installation Process
Before commencing with the installation of a wafer check valve, it's crucial to undertake the following preparatory steps:
Installation Considerations
Installing wafer check valves requires careful consideration of various factors to ensure optimal performance and longevity. Here are key considerations to keep in mind:
Regular Maintenance
Regular maintenance of wafer check valves is essential to ensure their continued optimal performance and longevity. Here's a comprehensive guide to regular maintenance:
Choosing Installation Location
Regarding whether to install before or after gate valves, consider the following:
By adhering to proper installation and regular maintenance procedures, wafer check valves can ensure their normal operation and performance stability, enhancing the reliability of pipeline systems and ensuring operational safety. Moreover, strict adherence to relevant operational protocols and safety guidelines during installation and maintenance is essential to ensure the safety of personnel.
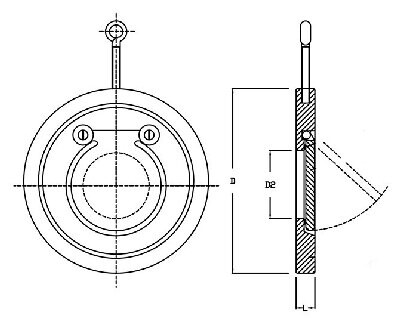
Pre-Installation Preparations
Before proceeding with the installation of wafer check valves, it is essential to undertake thorough pre-installation preparations to ensure a successful and effective installation process. These preparations include:
- Inspect Valve Integrity: Thoroughly examine the exterior of the wafer check valve to ensure there are no visible damages or deformations, guaranteeing its proper functioning.
- Clean Installation Area: Clean the installation area to ensure the pipeline surface is free from debris and dirt, facilitating a secure clamping effect and connection.
- Adjust Clamping Force: Adjust the clamping force according to the valve specifications and pipeline size to ensure a stable connection that prevents leaks or loosening.
Installation Process
Before commencing with the installation of a wafer check valve, it's crucial to undertake the following preparatory steps:
- Clamping Fixation: Select an appropriate clamping method based on the valve diameter and pipeline specifications, ensuring even distribution of clamping force for a sealed connection between the valve and the pipeline.
- Connect Pipelines: Use pipe fittings of corresponding sizes to connect the wafer check valve to the pipeline, ensuring a secure and reliable connection to prevent leakage or other issues.
Installation Considerations
Installing wafer check valves requires careful consideration of various factors to ensure optimal performance and longevity. Here are key considerations to keep in mind:
- Consistent Flow Direction: Ensure the flow direction through the wafer check valve is consistent with the fluid flow to avoid installation errors that could lead to functional failure.
- Use of Expansion Joints: Use expansion joints between the wafer check valve and other valves instead of direct connections to reduce pipeline vibrations and impact forces.
- Avoid Obstructions: Avoid installing pipe fittings or obstructions within the operating radius of the valve disc to ensure proper valve function.
- Positioning: Avoid installing reducers directly before or after the wafer check valve to maintain its effectiveness.
- Adequate Space: Provide sufficient space, especially near bends, when installing wafer check valves to ensure smooth operation.
- Outlet Space for Pump: When installing wafer check valves at pump outlets, ensure at least six times the valve diameter of space to withstand fluid forces on the valve disc.
Regular Maintenance
Regular maintenance of wafer check valves is essential to ensure their continued optimal performance and longevity. Here's a comprehensive guide to regular maintenance:
- Cleaning and Maintenance: Regularly clean the interior of the valve and pipeline system, especially the valve disc and sealing surfaces, to prevent buildup of debris and corrosion, ensuring smooth valve operation.
- Seal Inspection: Periodically inspect the valve disc and sealing surfaces for signs of wear and tear, and promptly replace any damaged or worn components to maintain sealing performance.
- Operational Testing: Conduct periodic operational tests on the wafer check valve to ensure its opening and closing are flexible and reliable, ensuring its normal operation.
- Leakage Check: Regularly check for any leakage in the wafer check valve, and if detected, take immediate measures to address the issue to maintain system integrity and safety.
Choosing Installation Location
Regarding whether to install before or after gate valves, consider the following:
- Before Gate Valve: Installing before gate valves can protect them by bearing the impact force. However, if the flow rate is unstable, it may affect the lifespan of the wafer check valve.
- After Gate Valve: Installing after gate valves can protect wafer check valves, especially in parallel pump systems, facilitating repairs. However, long-term exposure to high-pressure water impact may damage gate valves, so it's preferable to select wafer check valves that reduce water hammer effects.
By adhering to proper installation and regular maintenance procedures, wafer check valves can ensure their normal operation and performance stability, enhancing the reliability of pipeline systems and ensuring operational safety. Moreover, strict adherence to relevant operational protocols and safety guidelines during installation and maintenance is essential to ensure the safety of personnel.
Cледующий: Устранение распространенных неисправностей шаровых клапанов в промышленных трубопроводах
Предыдущий: Кованый шаровой клапан из нержавеющей стали: передовая технология
О нас
Продукция
Навигация
Our Contacts
Building 2, NO.59, Songshan Road, SND, Suzhou, China