введение в общие структуры кузова шарового клапана
Oct 17, 2024
On this page
Ball valves are a common type of fluid control device, widely used in industries such as oil, gas, chemical processing, power generation, and water supply due to their simplicity, good sealing performance, and long service life. Depending on the valve body structure, ball valves can be categorized into top-entry, two-piece, three-piece, and fully welded types. Each type has its own design advantages and limitations, making it crucial to select the appropriate ball valve for reliable system operation and maintenance. This article will discuss the features, applications, and suitability of various ball valve types in real-world conditions.
Top-entry ball valves are designed so that the ball and other internal components can be accessed and removed from the top of the valve without taking the entire valve out of the pipeline. Compared to traditional side-entry ball valves, this design greatly simplifies maintenance, especially in high-pressure and large-diameter pipelines. These valves are commonly used in systems that require frequent maintenance or inspection, such as large-scale equipment in the oil and gas, chemical, and power industries.
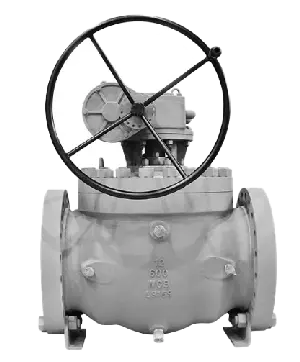
In-line maintenance: Internal components can be replaced or repaired without removing the valve from the pipeline, reducing downtime.
Suitable for large diameters and high-pressure applications: The top-entry design simplifies maintenance in large valves or high-pressure systems, especially when heavy machinery is needed for handling.
Long service life and high reliability: The ease of maintenance extends the valve's lifespan and reduces overall maintenance costs.
Increased weight and size: The complex structure of top-entry valves can increase their size and weight by 15%–30%, requiring stronger pipeline supports.
Higher cost: Although top-entry valves make maintenance easier, they come with higher initial purchase and installation costs, particularly in systems that don't require frequent maintenance.
Limited application: Some specialized valves with complex internal parts, like trunnion-mounted ball valves, require a top-entry design to function properly.
Two-piece ball valves consist of two separate parts: a valve body with end connections and a matching piece. This type of valve has a simpler design and is generally used in small- to medium-sized applications. Since the valve body is composed of two parts, installation and maintenance require shutting down the system and removing the valve from the pipeline, making it more suited for applications with minimal maintenance needs.
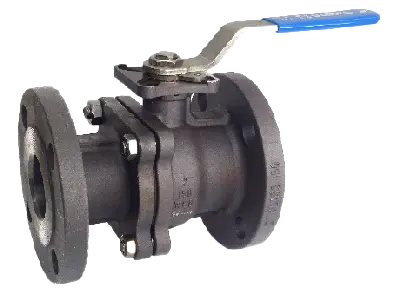
Lower cost: The simple structure of two-piece ball valves results in lower manufacturing and purchase costs, making them ideal for budget-conscious projects.
Durable construction: The design is sturdy and well-suited for systems with moderate pressure and temperature requirements.
Inconvenient maintenance: Maintenance requires completely removing the valve, leading to increased downtime and reduced system efficiency.
Three-piece ball valves consist of a valve body and two end caps. The end caps can be welded or threaded to the pipeline, while the valve body can be removed without disconnecting the end caps. This makes three-piece ball valves easier to maintain and clean, especially in applications that require frequent inspections, thereby reducing downtime.
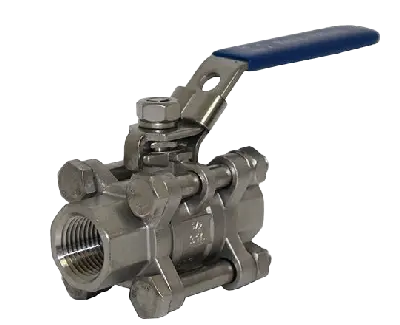
Easy maintenance: The valve body can be removed without disturbing the end caps, reducing downtime and simplifying maintenance procedures.
Wide range of applications: Suitable for industries requiring frequent cleaning and inspections, such as food processing, pharmaceuticals, and chemicals.
Higher initial cost: The more complex structure of three-piece ball valves results in higher material and manufacturing costs, particularly in high-pressure, high-temperature, or corrosive environments.
Fully welded ball valves feature an all-welded structure where the valve body is welded directly to the pipeline, eliminating the need for traditional flange connections. This design minimizes the risk of leaks and significantly reduces the valve's overall weight, making it ideal for large-scale, high-reliability applications like long-distance pipelines.
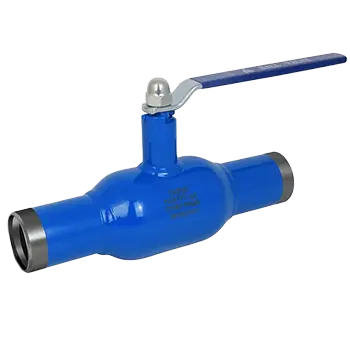
Excellent sealing performance: The fully welded structure eliminates potential leakage points from flanged connections, making it suitable for transporting high-pressure, high-temperature, or corrosive media.
Lightweight design: Without flanges or bolts, fully welded ball valves are significantly lighter, reducing the need for heavy-duty pipe supports and lowering overall project costs.
Corrosion resistance: These valves are ideal for transporting natural gas, oil, and other corrosive media, reducing the need for frequent maintenance.
Non-repairable: Once a fully welded ball valve's internal components are damaged, the valve cannot be repaired and must be replaced entirely, increasing long-term costs. Therefore, pipes must be thoroughly cleaned before installation to avoid damage from debris.
Complex manufacturing process: Fully welded ball valves require strict welding and heat treatment procedures, particularly for thicker walls, where post-weld heat treatment is necessary to relieve stress and ensure durability.
Selecting the appropriate ball valve type depends on specific operating conditions and maintenance requirements.
Top-entry ball valves are ideal for large systems that require frequent maintenance, especially in high-pressure and large-diameter pipelines. Their in-line maintenance capability saves time and reduces maintenance costs.
Two-piece ball valves are best suited for budget-conscious projects in small- to medium-sized systems that do not require frequent maintenance, although their maintenance process is more complex.
Three-piece ball valves are a good choice for applications requiring frequent cleaning and inspection, such as the food, pharmaceutical, and chemical industries. Their design reduces downtime during maintenance.
Fully welded ball valves are widely used in high-demand applications like long-distance pipelines due to their excellent sealing performance and lightweight design, making them ideal for transporting natural gas, oil, and other corrosive media.
Choosing the right ball valve type can optimize system performance, reduce maintenance costs, and extend the lifespan of equipment. Each type of ball valve—top-entry, two-piece, three-piece, and fully welded—has its own advantages and ideal applications. Evaluating the operating conditions, system requirements, and maintenance strategies is key to ensuring the reliability and efficiency of fluid control systems. By understanding the characteristics and applications of different ball valves, users can make more informed decisions for long-term system stability and performance.
Cледующий: применение обработки закалки в промышленных клапанах
Предыдущий: верхняя герметичность запорных клапанов и их оптимизация
О нас
Продукция
Навигация
Our Contacts
Building 2, NO.59, Songshan Road, SND, Suzhou, China