The Unrivaled Simplicity and Convenience of Three-Piece Ball Valves
Dec 15, 2023
The three-piece ball valve, a common structural configuration in the realm of ball valves, stands out for its straightforward design and practicality. Comprising a main valve body sandwiched between two subsidiary valve bodies, this valve structure facilitates easy installation and disassembly. Widely adopted in both floating and fixed ball valve systems, the three-piece design provides flexibility and efficiency.
1.Structural Diversity
The connection methods of the three-piece ball valve are diverse, offering options such as flange connection, threaded connection, welding, clamp connection, and socket connection. Material choices range from WCB cast steel to 304 and 316 stainless steel. Notably, this valve configuration finds widespread use in welded ball valves, where the ease of disassembly after welding allows for convenient replacement of the valve seat sealing ring. This makes the three-piece ball valve particularly suitable for scenarios with frequent switching and rapid wear.
2. Advantages of the Three-Piece Ball Valve
3. Applications and Adaptability:
The three-piece ball valve allows for the incorporation of a high-platform ball valve structure. It can be seamlessly integrated with pneumatic or electric actuators, forming pneumatic or electric three-piece ball valves. This adaptability not only simplifies installation but also streamlines maintenance procedures. Moreover, the larger flow channel dimensions of the three-piece ball valve's sphere compared to the one-piece ball valve result in enhanced flow capacity.
4. Installation Guidelines for Optimal Performance
In conclusion, the three-piece ball valve stands as a testament to simplicity, reliability, and adaptability in fluid control systems. Its user-friendly design, coupled with a range of advantageous features, positions it as a preferred choice across diverse industrial applications, where efficiency and ease of maintenance are paramount.
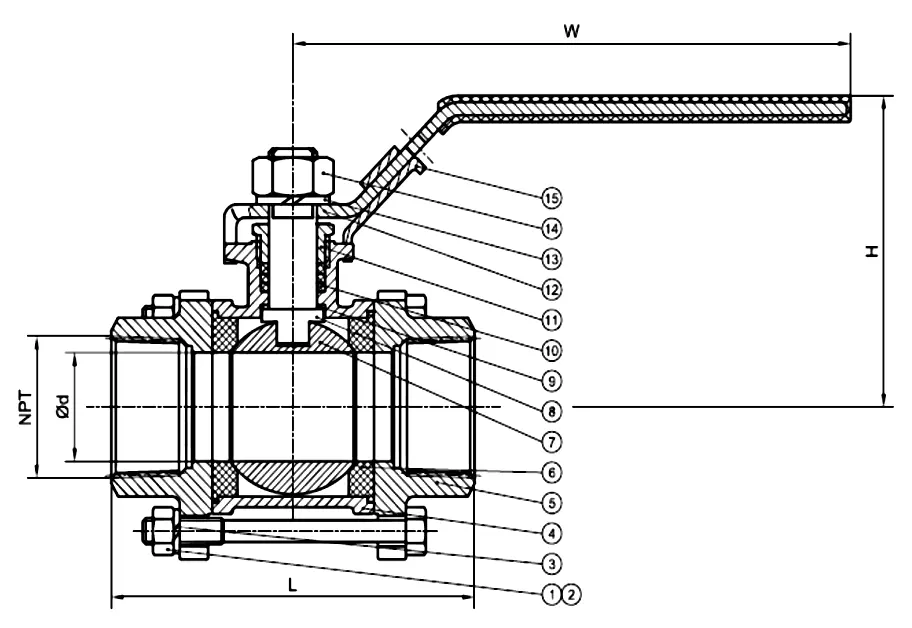
1.Structural Diversity
The connection methods of the three-piece ball valve are diverse, offering options such as flange connection, threaded connection, welding, clamp connection, and socket connection. Material choices range from WCB cast steel to 304 and 316 stainless steel. Notably, this valve configuration finds widespread use in welded ball valves, where the ease of disassembly after welding allows for convenient replacement of the valve seat sealing ring. This makes the three-piece ball valve particularly suitable for scenarios with frequent switching and rapid wear.
2. Advantages of the Three-Piece Ball Valve
Minimal Fluid Resistance: The valve exhibits low fluid resistance, with a resistance coefficient equivalent to that of a pipe segment of the same length.
Simplicity of Structure: Featuring a simple structure, compact size, and lightweight construction.
Reliability: The valve ensures a secure and reliable seal, with sealing surfaces commonly made of plastic, contributing to excellent sealing performance, even in vacuum systems.
Convenient Operation: The valve operates swiftly, requiring only a 90° rotation from fully open to fully closed, facilitating remote control over long distances.
Ease of Maintenance: With a straightforward structure and generally movable sealing rings, disassembly and replacement are straightforward tasks.
Isolation of Sealing Surfaces: When fully open or fully closed, the sealing surfaces of the ball and valve seat are isolated from the medium flow, preventing erosion of the valve sealing surface.
Simplicity of Structure: Featuring a simple structure, compact size, and lightweight construction.
Reliability: The valve ensures a secure and reliable seal, with sealing surfaces commonly made of plastic, contributing to excellent sealing performance, even in vacuum systems.
Convenient Operation: The valve operates swiftly, requiring only a 90° rotation from fully open to fully closed, facilitating remote control over long distances.
Ease of Maintenance: With a straightforward structure and generally movable sealing rings, disassembly and replacement are straightforward tasks.
Isolation of Sealing Surfaces: When fully open or fully closed, the sealing surfaces of the ball and valve seat are isolated from the medium flow, preventing erosion of the valve sealing surface.
3. Applications and Adaptability:
The three-piece ball valve allows for the incorporation of a high-platform ball valve structure. It can be seamlessly integrated with pneumatic or electric actuators, forming pneumatic or electric three-piece ball valves. This adaptability not only simplifies installation but also streamlines maintenance procedures. Moreover, the larger flow channel dimensions of the three-piece ball valve's sphere compared to the one-piece ball valve result in enhanced flow capacity.
4. Installation Guidelines for Optimal Performance
a. Pre-Installation Preparation: Thoroughly flush and clean the valve in the fully open state, ensuring the removal of protective covers on both flange ends. This initial step is crucial to establish a clean and debris-free foundation for the installation process.
b. System Validation: Conduct a comprehensive system test in accordance with specified signals, be they electric or pneumatic. This meticulous testing phase is essential to verify the optimal functionality of the valve before initiating the online installation, ensuring a smooth integration into the fluid control system.
c. Pipeline Preparations: Before connecting with the pipeline, execute a thorough flush and cleaning of the pipeline. This proactive measure aims to eliminate any impurities that may jeopardize the integrity of the valve seat and ball, safeguarding the longevity of the entire system.
d. Caution during Installation: Exercise caution by avoiding the use of the valve's actuator section as a lifting point during installation. This precautionary measure mitigates the risk of potential damage to the actuator and associated accessories, preserving the overall functionality of the valve.
e. Proper Orientation: Adhere to the specified orientation requirements for installation, whether horizontal or vertical. Following the designated orientation guidelines ensures the optimal performance of the valve, aligning it precisely with its intended operational parameters.
f. Environmental Considerations: Prioritize the selection of an installation point devoid of low-hanging or externally force-bearing elements. If such elements are present, employ pipe supports or braces as necessary. This foresighted approach guarantees a secure and stable installation environment, minimizing external factors that could impact the valve's performance.
g. Secure Connection: Upon connecting with the pipeline, employ the prescribed torque-cross locking method to securely fasten the flange connection bolts. This standardized tightening approach not only ensures a robust connection but also contributes to the overall safety and reliability of the installed valve.
b. System Validation: Conduct a comprehensive system test in accordance with specified signals, be they electric or pneumatic. This meticulous testing phase is essential to verify the optimal functionality of the valve before initiating the online installation, ensuring a smooth integration into the fluid control system.
c. Pipeline Preparations: Before connecting with the pipeline, execute a thorough flush and cleaning of the pipeline. This proactive measure aims to eliminate any impurities that may jeopardize the integrity of the valve seat and ball, safeguarding the longevity of the entire system.
d. Caution during Installation: Exercise caution by avoiding the use of the valve's actuator section as a lifting point during installation. This precautionary measure mitigates the risk of potential damage to the actuator and associated accessories, preserving the overall functionality of the valve.
e. Proper Orientation: Adhere to the specified orientation requirements for installation, whether horizontal or vertical. Following the designated orientation guidelines ensures the optimal performance of the valve, aligning it precisely with its intended operational parameters.
f. Environmental Considerations: Prioritize the selection of an installation point devoid of low-hanging or externally force-bearing elements. If such elements are present, employ pipe supports or braces as necessary. This foresighted approach guarantees a secure and stable installation environment, minimizing external factors that could impact the valve's performance.
g. Secure Connection: Upon connecting with the pipeline, employ the prescribed torque-cross locking method to securely fasten the flange connection bolts. This standardized tightening approach not only ensures a robust connection but also contributes to the overall safety and reliability of the installed valve.
In conclusion, the three-piece ball valve stands as a testament to simplicity, reliability, and adaptability in fluid control systems. Its user-friendly design, coupled with a range of advantageous features, positions it as a preferred choice across diverse industrial applications, where efficiency and ease of maintenance are paramount.
Next: API 607 Fire Safe Qualification Range for Valves
Previous: Floating Ball Valves: Structure, Features and Safety Design
About Us
Categories
Useful Links
Our Contacts
Building 2, NO.59, Songshan Road, SND, Suzhou, China