Managing Common Ball Valve Failures in Industrial Pipelines
Feb 29, 2024
Ball valves are prevalent control valves in industrial pipelines, favored for their simplistic design, minimal flow resistance, and superior sealing capabilities. However, akin to any mechanical apparatus, ball valves can encounter common failures over time, encompassing valve sticking, leakage, and seepage. This article delves into these typical ball valve issues and their rectification, while also exploring proactive strategies to ensure seamless industrial operations.
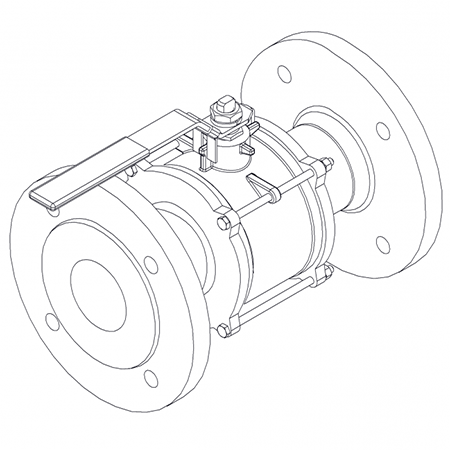
1. Valve Sticking
Long periods of inactivity or restricted movement can cause ball valves to become stuck, impeding their functionality. Sticking may arise from diverse factors, such as foreign objects or debris obstructing the valve, or deviations in the valve stem or worn sealing surfaces. Initial steps involve clearing obstructions caused by foreign objects or debris. Yet, if sticking results from stem deviations or worn sealing surfaces, repair or replacement of pertinent components becomes imperative.
2. Leakage Concerns
Leakage represents a prevalent challenge with ball valves, often attributable to several causes. Primarily, damage to sealing surfaces is a common culprit. Prolonged use can lead to surface abrasion, compromising sealing effectiveness. Additionally, aging of sealing gaskets can contribute to leakage, as aged gaskets lose elasticity and fail to tightly conform to the valve. Loose fasteners on the ball valve, such as screws or nuts, can also lead to leakage. Lastly, improper installation can exacerbate leakage issues.
Addressing leakage demands diverse approaches contingent on the situation. Common corrective measures include replacing sealing surfaces and gaskets. Vital steps also encompass checking and tightening fasteners. If leakage stems from improper installation, reinstallation of the ball valve becomes necessary.
3. Seepage Challenges
Seepage stands as another common issue with ball valves, potentially resulting from aging sealing gaskets, damaged sealing components, or ball deformation. These issues compromise the valve's sealing performance, leading to medium leakage and disrupting regular industrial processes.
Remedying seepage follows a similar approach to addressing leakage. Principal repair methods include replacing sealing gaskets and components. In cases of ball deformation, replacement is the sole solution to resolve seepage.
4. Prevention and Maintenance
To avert disruptions caused by ball valve failures in industrial operations, stringent preventive measures and regular maintenance are indispensable. Regular inspection of ball valve operation ensures unimpeded movement, effectively preventing valve sticking. Periodic replacement of sealing surfaces and gaskets, along with tightening fasteners, safeguards the valve's sealing performance. Adherence to installation requirements is vital in preventing leakage issues.
In summary, while ball valve failures are commonplace, timely troubleshooting and preventive measures can ensure smooth valve operation, safeguarding the efficiency and safety of industrial processes. Therefore, consistent maintenance and proactive measures for ball valves in industrial pipelines are essential. These practices not only extend the service life of ball valves but also enhance the safety and efficiency of industrial operations.
Next: Comparing Rising and Non-Rising Stem Gate Valves
Previous: Ensuring Safe and Stable Installation of Wafer Check Valves
About Us
Categories
Useful Links
Our Contacts
Building 2, NO.59, Songshan Road, SND, Suzhou, China