¿Cuáles son las ventajas de las válvulas de bronce de níquel-aluminio?
May 19, 2023
Aluminum bronze valves are highly suitable for corrosive, saline environments. The common specification is ASTM B148 C95800 although the AB2 specification is also used. These are similar to C95500 and C95400 specifications and offer good castability, reasonable bearing material, easy machining and high tensile strength.
Aluminum-bronze valves are a suitable and far cheaper substitute to duplex, super duplex, and monel for many seawater applications, especially in low-pressure applications. Its major drawback is its low tolerance to heat. Aluminium-bronze is also referred to as nickel-aluminum bronze and abbreviated as NAB.
Aluminum bronze material introduction
C95800 offers superior saltwater corrosion resistance. It also is resistant to cavitation and erosion. Along with the advantage of pressure tightness, this high-strength alloy is excellent for welding and is available in many forms at a lower cost to you. So NAB C95800 Globe valves are typically used for shipbuilding with seawater or fire water application.
Aluminum bronze is a type of bronze in which aluminum is the main alloying metal added to copper. A variety of aluminum bronzes of differing compositions have found industrial use, with most ranging from 5% to 11% aluminum by weight, the remaining mass being copper; other alloying agents such as iron, nickel, manganese, and silicon are also sometimes added to aluminum bronzes.
Aluminum Bronze Alloys are important materials due to their excellent physical, mechanical, anti-corrosive, and wearing properties. Add Nickel to the alloy and you can achieve an increase in strength without diminishing it’s excellent ductility, toughness, and corrosion resistance.
Nickel Aluminum Bronze Alloys are used in a wide array of components in many different industries. Normally specified for their high strength, good wear resistance, abrasion resistance, and excellent resistance to corrosion in seawater and many other aggressive environments.
The corrosion-resistant property relies on the formation of a copper/aluminum oxide film. This film is self-repairing in media containing even low levels of oxygen.
This oxide film provides the following benefits:
-It adheres firmly to the surface of the substrate
-It has a resistance to liquid penetration
-The hardness of the alumina content creates higher resistance to erosion and abrasion
Nickel Aluminum Bronze alloys can be considered for service in the following chemicals. The selection must take into account the operational temperature, concentrations, service conditions, and impurities.
High Strength - Good wear and abrasion resistance. With the addition of Nickel can be achieved without diminishing ductility
Corrosion resistant - Especially in seawater and in various chemical environments
Excellent physical and mechanical properties that can be improved via various thermal treatments
Applications for Nickel Aluminum Bronze Valves
The various types of nickel aluminum bronze alloys are a popular choice for industrial applications such as landing gear bushings and bearings for the aerospace industry, propeller hubs, wear rings, and hardware for the marine industry, piping for vertical pump columns, firefighting and fire suppression systems, and seawater lift pumps for the oil and gas industry, hydraulic bushings for earth moving equipment, as well as many other applications. This is due specifically to the addition of nickel which improves the corrosion resistance of the already versatile aluminum bronze alloys. Iron acts as a grain refiner and increases tensile strength without diminishing its excellent ductility and toughness.
Aluminum bronzes are most commonly used in applications where their resistance to corrosion makes them preferable to other engineering materials. These applications include plain bearings and landing gear components on aircraft, engine components (especially for seagoing ships), underwater fastenings in naval architecture, and ship propellers. The attractive gold-toned coloration of aluminum bronzes has also led to their use in jewelry.
Aluminum bronzes are in the highest demand from the following industries and areas:
-General sea water-related service
-Water supply
-Oil and petrochemical industries eg tools for use in non-sparking environments
-Specialized anti-corrosive applications
-Certain structural retrofit building applications
C95800 Valves
-cost-effective (cheaper than the exotic alternatives);
- long-lasting (comparable in performance on general corrosion, pitting, and cavitation to super duplex alloys and significantly better than the standard alloys), and
-a good valve material (does not gall, has excellent anti-fouling properties, and is a good thermal conductor), makes it an excellent choice for valves in seawater service.
Common used Valve Material Construction
Body, Bonnet, Disc Cast Ni-Alu bronze ASTM B148-C95800
Stem, Back Seat Ring Alu-Bronze ASTM B150-C63200 or Monel 400
Gaskets & Packing Graphite or PTFE
Bolting, Fasteners Stainless Steel A194-8M & A193-B8M
Hand Wheel Cast Iron A536+Anti-corrosive plastic
Material properties
Aluminum bronzes are most valued for their higher strength and corrosion resistance as compared to other bronze alloys. These alloys are tarnish-resistant and show low rates of corrosion in atmospheric conditions, low oxidation rates at high temperatures, and low reactivity with sulfurous compounds and other exhaust products of combustion. They are also resistant to corrosion in seawater. Aluminum bronze's resistance to corrosion rests in the aluminum component of the alloys, which reacts with atmospheric oxygen to form a thin, tough surface layer of alumina (aluminum oxide) which acts as a barrier to corrosion of the copper-rich alloy.
Another notable property of aluminum bronzes is their biostatic effects. The copper component of the alloy prevents colonization by marine organisms including algae, lichens, barnacles, and mussels, and therefore can be preferable to stainless steel or other non-cupric alloys in applications where such colonization would be unwanted. Aluminum bronzes tend to have a golden color.
ASTM B148
ASTM B150
ASTM B271
ASTM B584
If you need any support please contact Bosseal team.
Aluminum-bronze valves are a suitable and far cheaper substitute to duplex, super duplex, and monel for many seawater applications, especially in low-pressure applications. Its major drawback is its low tolerance to heat. Aluminium-bronze is also referred to as nickel-aluminum bronze and abbreviated as NAB.
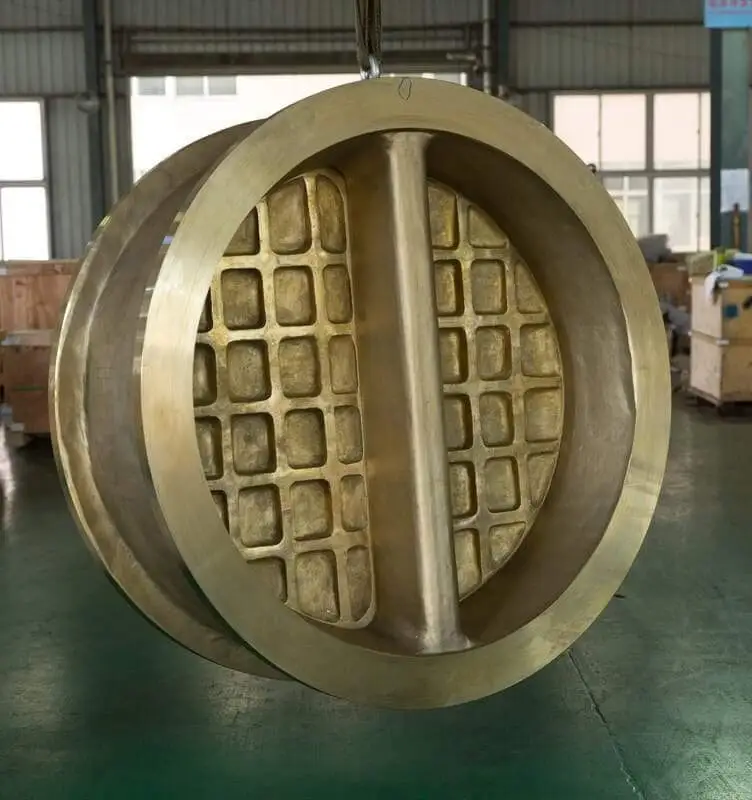
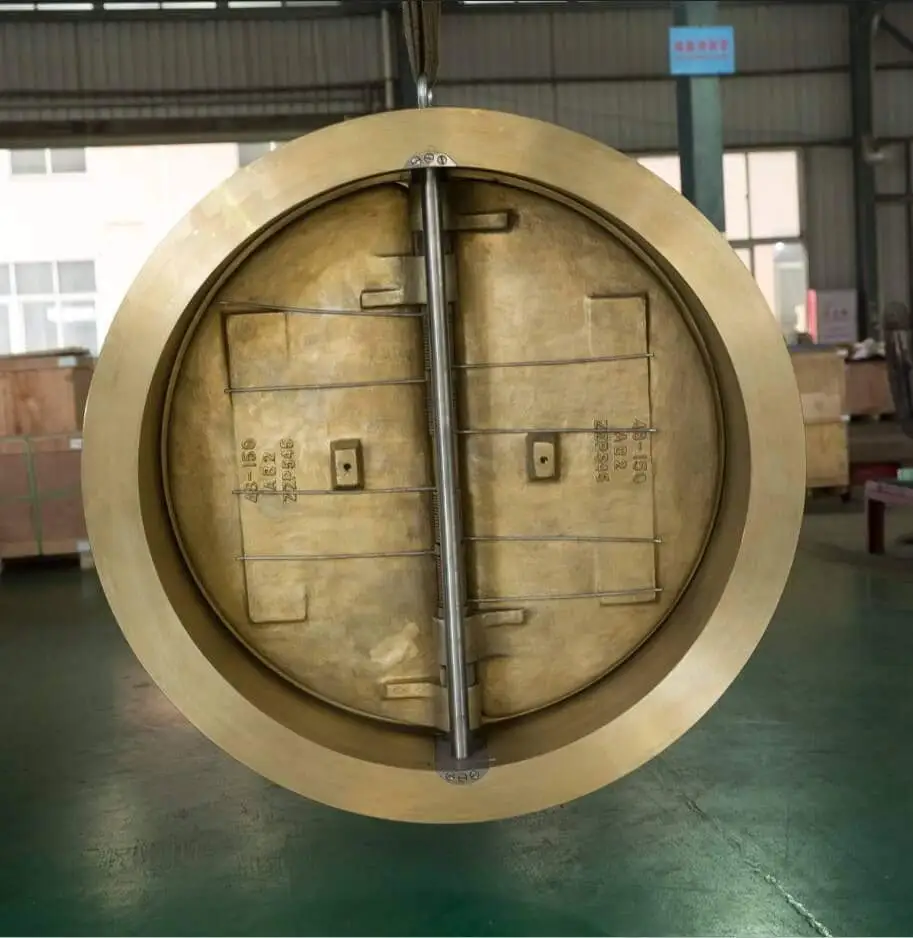
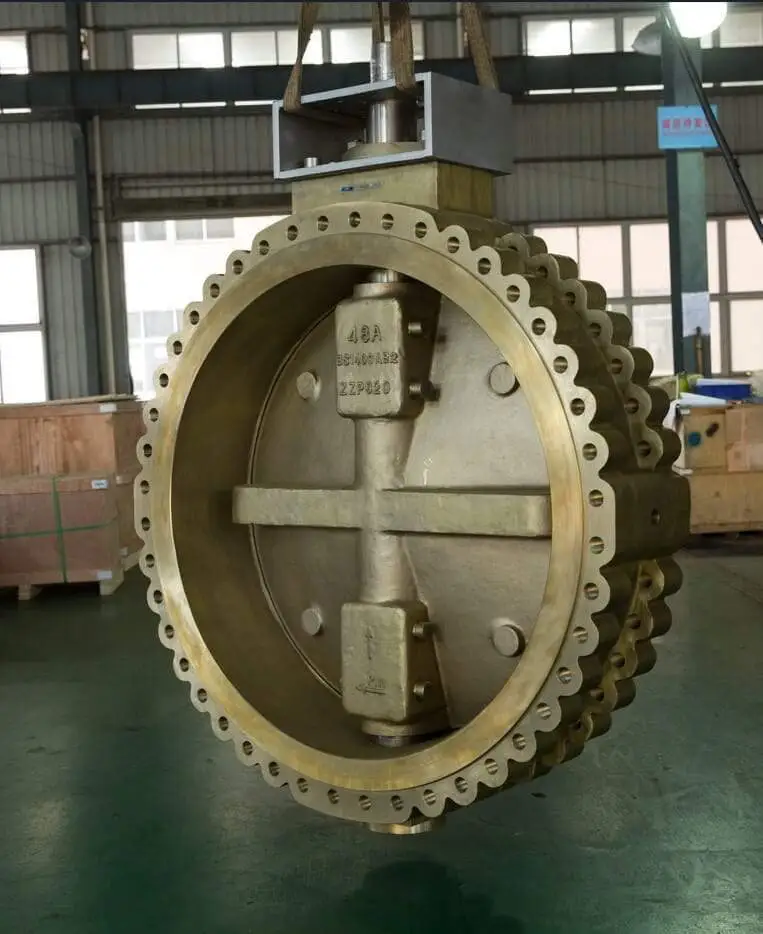
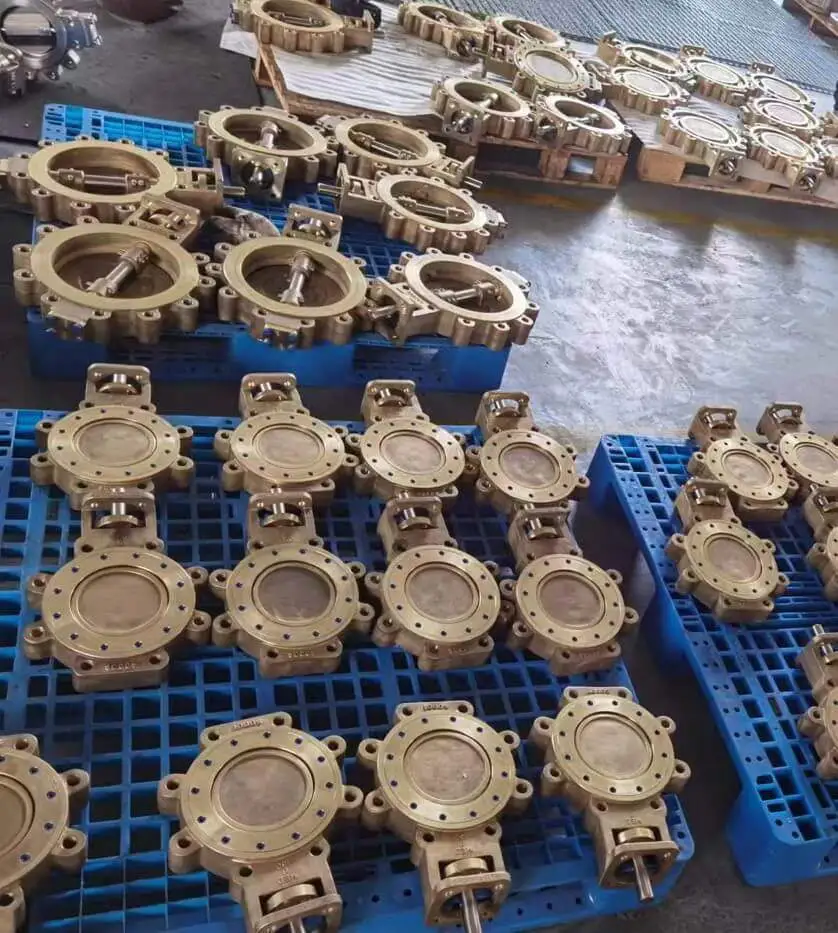
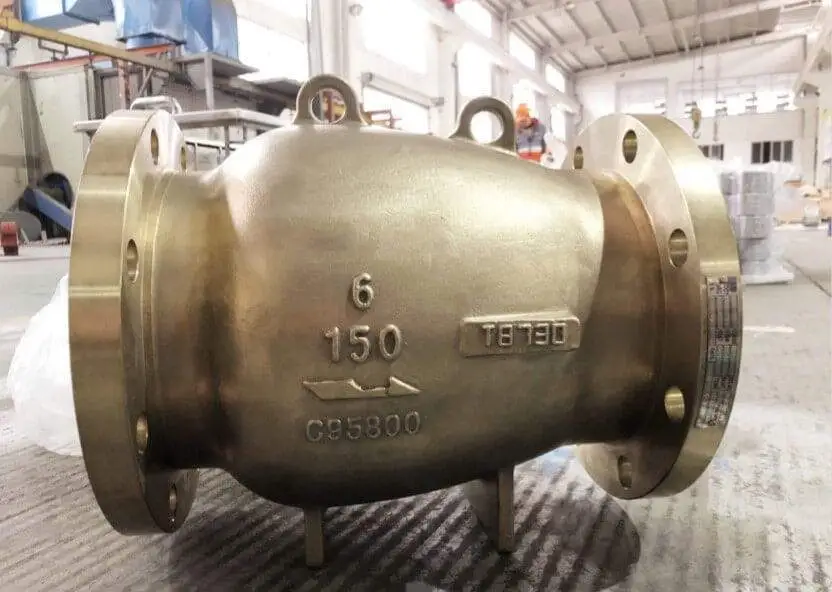
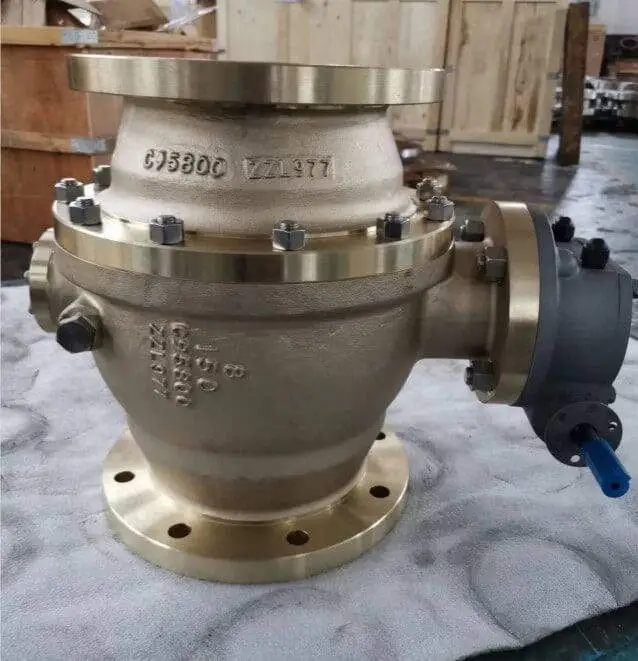
Aluminum bronze material introduction
C95800 offers superior saltwater corrosion resistance. It also is resistant to cavitation and erosion. Along with the advantage of pressure tightness, this high-strength alloy is excellent for welding and is available in many forms at a lower cost to you. So NAB C95800 Globe valves are typically used for shipbuilding with seawater or fire water application.
Aluminum bronze is a type of bronze in which aluminum is the main alloying metal added to copper. A variety of aluminum bronzes of differing compositions have found industrial use, with most ranging from 5% to 11% aluminum by weight, the remaining mass being copper; other alloying agents such as iron, nickel, manganese, and silicon are also sometimes added to aluminum bronzes.
Aluminum Bronze Alloys are important materials due to their excellent physical, mechanical, anti-corrosive, and wearing properties. Add Nickel to the alloy and you can achieve an increase in strength without diminishing it’s excellent ductility, toughness, and corrosion resistance.
Nickel Aluminum Bronze Alloys are used in a wide array of components in many different industries. Normally specified for their high strength, good wear resistance, abrasion resistance, and excellent resistance to corrosion in seawater and many other aggressive environments.
The corrosion-resistant property relies on the formation of a copper/aluminum oxide film. This film is self-repairing in media containing even low levels of oxygen.
This oxide film provides the following benefits:
-It adheres firmly to the surface of the substrate
-It has a resistance to liquid penetration
-The hardness of the alumina content creates higher resistance to erosion and abrasion
Nickel Aluminum Bronze alloys can be considered for service in the following chemicals. The selection must take into account the operational temperature, concentrations, service conditions, and impurities.
High Strength - Good wear and abrasion resistance. With the addition of Nickel can be achieved without diminishing ductility
Corrosion resistant - Especially in seawater and in various chemical environments
Excellent physical and mechanical properties that can be improved via various thermal treatments
Applications for Nickel Aluminum Bronze Valves
The various types of nickel aluminum bronze alloys are a popular choice for industrial applications such as landing gear bushings and bearings for the aerospace industry, propeller hubs, wear rings, and hardware for the marine industry, piping for vertical pump columns, firefighting and fire suppression systems, and seawater lift pumps for the oil and gas industry, hydraulic bushings for earth moving equipment, as well as many other applications. This is due specifically to the addition of nickel which improves the corrosion resistance of the already versatile aluminum bronze alloys. Iron acts as a grain refiner and increases tensile strength without diminishing its excellent ductility and toughness.
Aluminum bronzes are most commonly used in applications where their resistance to corrosion makes them preferable to other engineering materials. These applications include plain bearings and landing gear components on aircraft, engine components (especially for seagoing ships), underwater fastenings in naval architecture, and ship propellers. The attractive gold-toned coloration of aluminum bronzes has also led to their use in jewelry.
Aluminum bronzes are in the highest demand from the following industries and areas:
-General sea water-related service
-Water supply
-Oil and petrochemical industries eg tools for use in non-sparking environments
-Specialized anti-corrosive applications
-Certain structural retrofit building applications
C95800 Valves
-cost-effective (cheaper than the exotic alternatives);
- long-lasting (comparable in performance on general corrosion, pitting, and cavitation to super duplex alloys and significantly better than the standard alloys), and
-a good valve material (does not gall, has excellent anti-fouling properties, and is a good thermal conductor), makes it an excellent choice for valves in seawater service.
Common used Valve Material Construction
Body, Bonnet, Disc Cast Ni-Alu bronze ASTM B148-C95800
Stem, Back Seat Ring Alu-Bronze ASTM B150-C63200 or Monel 400
Gaskets & Packing Graphite or PTFE
Bolting, Fasteners Stainless Steel A194-8M & A193-B8M
Hand Wheel Cast Iron A536+Anti-corrosive plastic
Material properties
Aluminum bronzes are most valued for their higher strength and corrosion resistance as compared to other bronze alloys. These alloys are tarnish-resistant and show low rates of corrosion in atmospheric conditions, low oxidation rates at high temperatures, and low reactivity with sulfurous compounds and other exhaust products of combustion. They are also resistant to corrosion in seawater. Aluminum bronze's resistance to corrosion rests in the aluminum component of the alloys, which reacts with atmospheric oxygen to form a thin, tough surface layer of alumina (aluminum oxide) which acts as a barrier to corrosion of the copper-rich alloy.
Another notable property of aluminum bronzes is their biostatic effects. The copper component of the alloy prevents colonization by marine organisms including algae, lichens, barnacles, and mussels, and therefore can be preferable to stainless steel or other non-cupric alloys in applications where such colonization would be unwanted. Aluminum bronzes tend to have a golden color.
- Excellent strength and ductility even at low temperatures
- Good casting qualities
- Excellent shock & wear resistance
- Good machinability
- Good thermal and electrical conductivity
- Suitable for welding
- Exceptional corrosion resistance
ASTM B148
ASTM B150
ASTM B271
ASTM B584
If you need any support please contact Bosseal team.
Siguiente: Válvula de bola de 28 pulgadas 300 libras lista para el envío
Anterior: ¿Cuál es la presión de fisuración de la válvula de retención?
Sobre nosotros
Categorías
Enlaces útiles
Our Contacts
Building 2, NO.59, Songshan Road, SND, Suzhou, China